What is the difference between forged and cast steel valves?
For a variety of industrial applications, cast and forged steel valves offer robust, high-performance flow control. Both production processes yield strong metal valve bodies, but the end products have differing characteristics that affect functionality and longevity. Finding the best answer is made possible by knowing how cast and forged valves differ from one another.
Melted steel is poured into molds to generate the necessary shapes for the production of cast steel valve bodies. As the steel cools within the mold cavity, it solidifies. As a result, the body is produced with a dense, isotropic substance that has consistent qualities throughout.
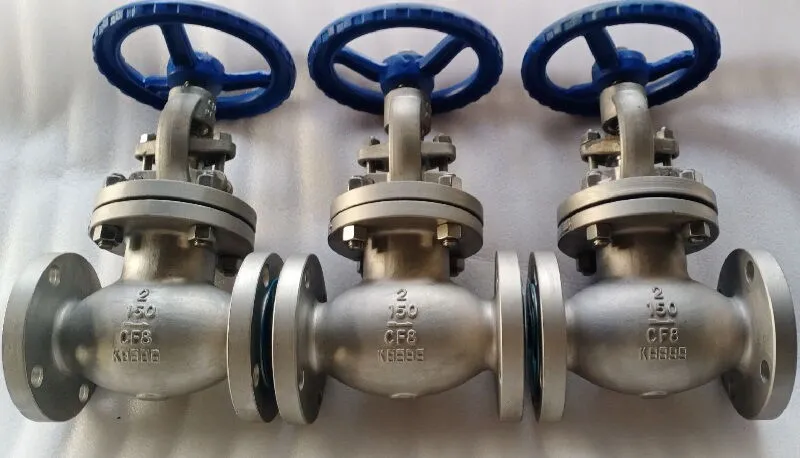
Important characteristics of cast steel valves are as follows:
- The economical manufacture of intricate patterns
- Outstanding dimensional accuracy and repeatability
- Compact, impenetrable microstructures
- Greater ratios of strength to weight
- In order to obtain final tolerances and interfaces, the as-cast surfaces typically need to be machined. Carbon and chrome/nickel alloy steels are common grades of cast steel. Heat treatment is one more way to improve the material's qualities.
Water and wastewater, fire safety, mining, and construction services are among the industries that frequently use cast steel valves. Tight shutoff responsibilities are well-suited for their exceptional sealing efficiency.
During the forging process, hot steel billets are mechanically pushed or hammered into shape. The strong compressive stresses cause the interior grain structure to realign. As a result, forged steel valve bodies have improved strength properties.
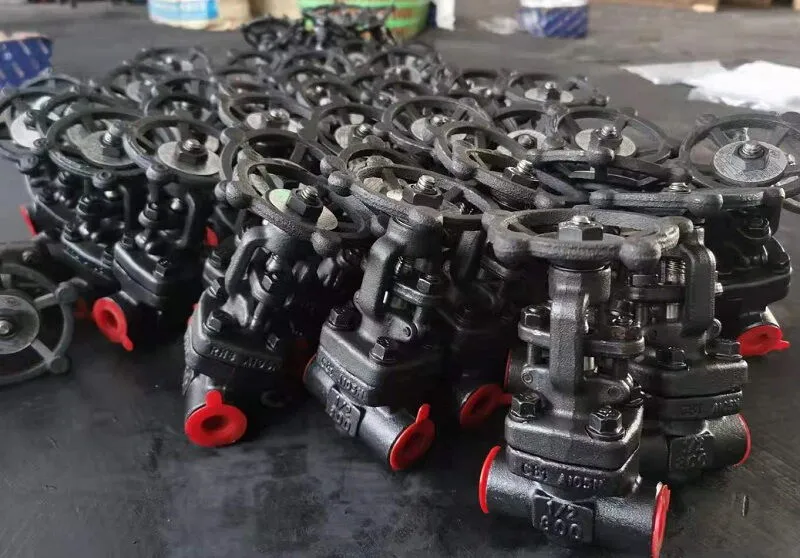
forged steel valves' features include:
- Greater ratings for tensile and yield strength
- Increased resilience and toughness
- Withstands exhaustion and stress cracking
- Withstands great pressure and extremely cold temperatures
- Diminished leakage rates when ΔP is large
- Additionally, the refined grain structure strengthens defenses against erosion and corrosion damage. Forgings are perfect for high integrity applications because of their continuous working and grain flow.
Nonetheless, considerable machining is necessary to finalize crucial sealing surfaces on a forged valve body. Common grades of forged steel include alloys including nickel, chromium, and molybdenum. Oil and gas, petrochemical and chemical, power generation, and other high-pressure/high-temperature services are among the top applications.
Key Differences Between Cast and Forged Valves
What are the differences between cast and forged steel valves in terms of cost, performance, and service life, taking into account their unique production processes?
A forged steel valve's strength is definitely an advantage. Steel's interior grain structure is realigned during the forging process, greatly increasing its strength. Forged valves are less prone to fail under sudden pressure changes or cycling and can withstand significantly higher pressures.
Forged steel valves are frequently used in oil, gas, chemical, and power facilities for applications involving extremely high pressure, where a valve failure could have disastrous consequences. Forged steel is less prone to break or crack even under extremely high pressure spikes or frequent cycles.
Up to about 1500 PSI, cast steel is unquestionably robust enough for a wide range of applications. In water, steam, gas, and chemical systems operating at modest pressures, cast steel valves with well-designed construction offer dependable performance. Forged steel, however, is the preferred material when the utmost integrity and durability are required.
There is a comparable distinction in terms of leaking. Forgings with a refined grain flow have fewer surface imperfections that might cause leaks. Forged valves usually have reduced leakage rates under extreme pressure differentials. Surface smoothness and improved tolerances between mating pieces are achieved through forging.
Small pores may occasionally be present on cast steel surfaces, even with a dense casting overall. Leak-tight seals are ensured by further machining, and contemporary casting controls further reduce this problem. Excellent shutdown can be achieved with cast steel valves as well as forged steel valves.
In terms of materials and manufacturing costs, forged steel valves are more expensive than their cast valve body counterparts. The billets made of raw materials cost more. In addition to requiring more energy to produce, forgings also require longer machining times to complete the components.
Conversely, casting allows valves to be produced at a lower cost and with shorter lead times. The procedure easily creates near-net shape complicated part geometries. As a result, less machining is done. All things considered, many industrial markets find cast steel valves to have appealing economics.
Forged steel is the obvious option in instances when valve performance supersedes budgetary considerations. A robust and sturdy material structure is produced by the refined forged grain. This guarantees dependable performance in extremes of temperature, pressure, and cyclic loading. The likelihood of leaks, fatigue failures, and other functional problems is reduced using forged steel.
Forged valves have greater material and production costs, therefore even with their performance advantages, they are not cost-effective for all applications. Cast steel valves can offer extremely capable service at significantly lower cost when pressure, temperature, and cycling characteristics are within modest limits.
High-quality valves at competitive prices are made possible by the casting process's dimensional uniformity and scalability. When used in non-extreme performance scenarios, cast steel is ideal for a variety of industrial sectors and operating environments.
One of the leading producers of forged and cast steel valves, JONLOO Valve assists clients in choosing the best production technique based on the needs, budget, and specifications of each application. To review the working conditions and system specifications, get in touch with us right now. JONLOO will advise on the best forged or cast steel valves to optimize value and dependability.
JONLOO Valve has the experience to provide the best cast and forged steel valves, regardless of the applications that call for the economy of premium castings or the strength and resilience of forgings. With integrated manufacturing facilities covering the whole production process, JONLOO ensures total quality control to guarantee dependable, long-lasting performance from both types of valves.
To adapt the valve production procedure to the service needs for new or retrofit projects,JONLOO combines considerable application knowledge with a thorough study of operating characteristics. For assistance choosing the best cast or forged steel valves for your unique pressure, temperature, fluid, and cycling requirements, get in touch with JONLOO Valve right now. JONLOO's extensive understanding in forged and cast valve materials, designs, and production will help you maintain safe and effective processes.