Most high end wrist watches like emphasizing their watch bracelet and watch case are made of 316L, 904L or Surgical Grade Stainless Steel. What are they?
Stainless Steel is not a single material but the name for a family of corrosion resistant steels.
Properties of Stainless Steels
The advantageous properties of stainless steel can be seen when compared to standard plain carbon mild steel. Although stainless steels have a broad range of properties, in general, when compared with carbon mild steel, stainless steels have:
- Higher corrosion resistance
- Higher cryogenic toughness
- Higher work hardening rate
- Higher hot strength
- Higher ductility
- Higher strength and hardness
- A more attractive appearance
- Lower maintenance
Corrosion Resistance of Stainless Steel
All stainless steel are iron-based alloys that contain a minimum of around 10.5% Chromium. The Chromium in the alloy forms a self-healing protective clear oxide layer. This oxide layer gives stainless steel their corrosion resistance. The self healing nature of the oxide layer means the corrosion resistance remains intact regardless of fabrication methods. Even if the material surface is cut or damaged, it will self heal and corrosion resistance will be maintained.
Conversely, normal carbon steels may be protected from corrosion by painting or other coatings like galvanizing. Any modification of the surface exposes the underlying steel and corrosion can occur.
The corrosion of different grades of stainless steel will differ with various environments. Suitable grades will depend upon the service environment. Even trace amounts of some elements can markedly alter the corrosion resistance. Chlorides in particular can have an adverse effect on the corrosion resistance of stainless steel.
Grades high in Chromium, Molybdenum and Nickel are the most resistant to corrosion.
Grade 316 is the standard molybdenum-bearing grade, second in importance to 304 amongst the austenitic stainless steels. The molybdenum gives 316 better overall corrosion resistant properties than Grade 304, particularly higher resistance to pitting and crevice corrosion in chloride environments. It has excellent forming and welding characteristics. It is readily brake or roll formed into a variety of parts for applications in the industrial, architectural, and transportation fields. Grade 316 also has outstanding welding characteristics. Post-weld annealing is not required when welding thin sections.
Grade 316L, the low carbon version of 316 and is immune from sensitization (grain boundary carbide precipitation). Thus it is extensively used in heavy gauge welded components (over about 6mm). Grade 316H, with its higher carbon content has application at elevated temperatures, as does stabilized grade 316Ti.
The austenitic structure also gives these grades excellent toughness, even down to cryogenic temperatures.
904L is a non-stabilised low carbon high alloy austenitic stainless steel. The addition of copper to this grade gives it greatly improved resistance to strong reducing acids, particularly sulphuric acid. It is also highly resistant to chloride attack - both pitting / crevice corrosion and stress corrosion cracking.
This grade is non-magnetic in all conditions and has excellent weldability and formability. The austenitic structure also gives this grade excellent toughness, even down to cryogenic temperatures.
904L does have very substantial contents of the high cost ingredients nickel and molybdenum. Many of the applications in which this grade has previously performed well can now be fulfilled at lower cost by duplex stainless steel 2205 (S31803 or S32205), so it is used less commonly than in the past
.904L Plug Valve is used a lot for chemical industry with high corrosive medium.
Martensitic Stainless Steels / Surgical grade stainless steels
High carbon and lower chromium content are the distinguishing features of martensitic stainless steel when compared with ferritic stainless.
Martensitic stainless steels include 410, 416, 420 and 440. Hardened martensitic steels cannot be successfully cold formed. They are magnetic, have moderate corrosion resistance and poor weldability.
For surgical grade application: 420, 440 are used.
Grade 420 stainless steel is a higher carbon version of 410; like most non-stainless steels it can be hardened by heat treatment. It contains a minimum of 12 per cent chromium, just sufficient to give corrosion resistance properties. It has good ductility in the annealed condition but is capable of being hardened up to Rockwell Hardness 50HRC, the highest hardness of the 12 per cent chromium grades. Its best corrosion resistance is achieved when the metal is hardened and surface ground or polished.
Related grades to 420 are high carbon high hardness martensitic stainless steels such as the 440 series and also variations to 420 containing molybdenum (for increased corrosion resistance), sulphur (for increased machinability) or vanadium (for higher hardness). A slightly higher carbon version of 420 is the non-standard grade 420C.
Grade 440C is capable of attaining, after heat treatment, the highest strength, hardness and wear resistance of all the stainless alloys. Its very high carbon content is responsible for these characteristics, which make 440C particularly suited to such applications as ball bearings and valve parts.
Grades 440A and 440B are identical except for slightly lower carbon contents (0.60 - 0.75% and 0.75 - 0.95% respectively); these have lower attainable hardnesses but slightly higher corrosion resistances. Although all three versions of this grade are standard grades, in practice 440C is more available than the A or B variants.
A free-machining variant 440F (UNS S44020) also exists, with the same high carbon content as 440C. Again this grade is not readily available in Australia.
Martensitic stainless steels are optimised for high hardness, and other properties are to some degree compromised. Fabrication must be by methods that allow for poor weldability and usually also allow for a final harden and temper heat treatment. Corrosion resistance is lower than the common austenitic grades, and their useful operating temperature range is limited by their loss of ductility at sub-zero temperatures and loss of strength by over-tempering at elevated temperatures.
Comparison among 316L, 904L, surgical grade stainless steels |
|
Composition ranges |
Grade |
|
C |
Mn |
Si |
P |
S |
Cr |
Mo |
Ni |
N |
Cu |
316 |
Min |
- |
- |
- |
0 |
- |
16.0 |
2.00 |
10.0 |
- |
- |
Max |
0.08 |
2.0 |
0.75 |
0.045 |
0.03 |
18.0 |
3.00 |
14.0 |
- |
- |
316L |
Min |
- |
- |
- |
- |
- |
16.0 |
2.00 |
10.0 |
- |
- |
Max |
0.03 |
2.0 |
0.75 |
0.045 |
0.03 |
18.0 |
3.00 |
14.0 |
0.10 |
- |
904L |
Min |
- |
- |
- |
- |
- |
19.0 |
4.0 |
23.0 |
- |
1.0 |
Max |
0.020 |
2.00 |
1.00 |
0.045 |
0.035 |
23.0 |
5.0 |
28.0 |
- |
2.0 |
420 |
Min |
0.15 |
- |
- |
- |
- |
12.0 |
- |
- |
- |
- |
Max |
- |
1.00 |
1.00 |
0.040 |
0.030 |
14.0 |
- |
- |
- |
- |
440A |
Min |
0.65 |
- |
- |
- |
- |
16.00 |
- |
- |
- |
- |
Max |
0.75 |
1.00 |
1.00 |
0.040 |
0.030 |
18.00 |
0.75 |
- |
- |
- |
440B |
Min |
0.75 |
- |
- |
- |
- |
16.00 |
- |
- |
- |
- |
Max |
0.95 |
1.00 |
1.00 |
0.040 |
0.030 |
18.00 |
0.75 |
- |
- |
- |
440C |
Min |
0.95 |
- |
- |
- |
- |
16.00 |
- |
- |
- |
- |
Max |
1.20 |
1.00 |
1.00 |
0.040 |
0.060 |
18.00 |
0.75 |
- |
- |
- |
|
|
|
Mechanical properties |
|
|
|
|
Hardness |
Grade |
Tempering
Temp. (°C) |
Tensile Strength
(MPa) min |
Yield Strength
0.2% Proof
(MPa) min |
Elongation
(% in 50mm)
min |
Rockwell B
(HR B) max
|
Brinell
(HB) max |
Impact
Charpy V
(J) |
316 |
- |
515 |
205 |
40 |
95 |
217 |
|
316L |
- |
485 |
170 |
40 |
95 |
217 |
|
904L |
- |
490 |
220 |
35 |
70-90 typical |
- |
|
|
|
|
|
|
|
|
|
440C |
204 |
2030 |
1900 |
4 |
59 |
- |
9 |
260 |
1960 |
1830 |
4 |
57 |
- |
9 |
316 |
1860 |
1740 |
4 |
56 |
- |
9 |
371 |
1790 |
1660 |
4 |
56 |
- |
9 |
|
|
|
Typical physical properties |
Grade |
Density
(kg/m3) |
Elastic
Modulus
(GPa) |
Mean Co-eff of Thermal
Expansion (μm/m/°C) |
Thermal
Conductivity
(W/m.K) |
Specific
Heat
0 - 100 °C
(J/kg.K) |
Elec
Resistivity
(nΩ.m) |
|
|
|
0 - 100 °C |
0 - 315 °C |
0 - 538 °C |
At 100 °C |
At 500 °C |
|
|
316 / L / H |
8000 |
193 |
15.9 |
16.2 |
17.5 |
16.3 |
21.5 |
500 |
740 |
|
|
|
|
|
|
|
|
|
|
|
|
|
|
|
|
At 20 °C |
At 500 °C |
|
|
904L |
8000 |
200 |
15 |
- |
- |
13 |
- |
500 |
850 |
|
|
|
|
|
|
|
|
|
|
|
|
|
|
|
|
At 100 °C |
At 500 °C |
|
|
420
(annealed
condition) |
7750 |
200 |
10.3 |
10.8 |
11.7 |
24.9 |
- |
460 |
550 |
|
|
|
|
|
|
|
|
|
|
|
|
|
|
|
|
At 100 °C |
At 500 °C |
|
|
440A/B/C |
7650 |
200 |
10.1 |
10.3 |
11.7 |
24.2 |
- |
460 |
600 |
|
|
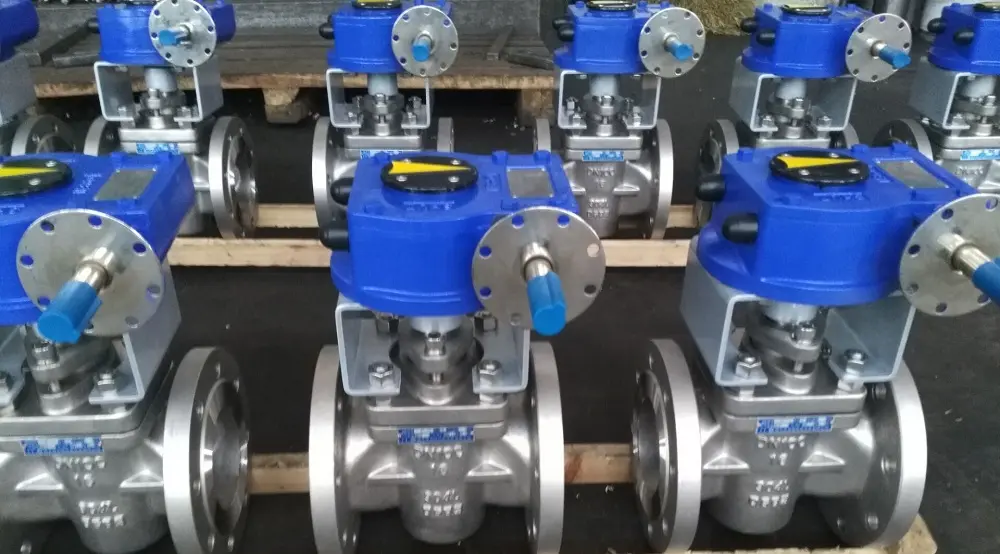