Structural Analysis & Design of a New Type of Ultra-low Temperature Floating Ball Valve (Part One)
Abstract: A new type of structural design plan of the ultra-low temperature floating ball valve was proposed based on the structural analysis of the existing common ultra-low temperature floating ball valve. The design difficulties of the eccentric distance of the ball and the wedge-shaped valve seat were analyzed, and the three-dimensional motion simulation verification was carried out. The sealing of the middle channel and stem of the ultra-low temperature valve was discussed, and suitable sealing can be selected for different media and pressure conditions. This new type of ultra-low temperature floating ball valve has simpler manufacturing and processing and good sealing performance, which can meet the harsh working conditions such as liquefied natural gas and promote the process of products made in China.
Introduction
In recent years, China's petrochemical industry has developed rapidly, especially natural gas. As the environmental problems caused by oil exploration have become more and more serious, natural gas has become an irreplaceable role in China's energy consumption and is widely used in people's production and life. Ultra-low temperature valves need to be used for transportation and storage of liquefied natural gas, which makes the demand for ultra-low temperature valves increase day by day, and puts forward higher requirements for ultra-low temperature valves.
Ultra-low temperature ball valves have been widely used in the transportation and storage of liquefied natural gas due to their advantages such as rapid opening and closing, low fluid resistance, and low noise. According to the form of the ball, the ball valve can be divided into two types: floating ball valves and trunnion ball valves. The ball of the floating ball valve is floating. Under the dual action of the medium pressure of the flow channel and initial sealing force, the ball can have a certain displacement to the outlet end and tightly press on the sealing surface of the valve seat at the outlet end to isolate the upstream medium to achieve a sealing effect; the ball of the fixed ball valve is fixed in the valve body and will not move in the valve body under the pressure of the medium. Sufficient initial sealing force and medium force are required to make the two sealing rings close to the spherical surface to keep the sealing.
The floating ball valve has small sizes, light weights, simple structure and good sealing, which is widely used in medium and low pressure and small diameter environments. However, there are not many common floating ball valve structures, mainly bevel types and side entry types due to the small flow passage of small-diameter ball valves and many internal processing restrictions. Floating ball valves with this structure have their own advantages and disadvantages, and can be used for some common working conditions. However, with the rapid development of the LNG industry in recent years, higher requirements have been put forward on ultra-low temperature valves, and some ball valves with new structure are required to meet the current increasingly harsh working conditions.
Through the analysis of the requirements of liquefied natural gas operations and the research on the shortcomings of the common structure of the floating ball valve, a new type of floating ball valve was designed, and its sealing performance and core components were analyzed and calculated; three-dimensional simulation was adopted. This new structure solves the problems of excessive torque, easy jamming, and difficulty in disassembly and assembly of common floating ball valves, and can be better applied to the complex working conditions of LNG.
1. Structural characteristics of common floating ball valves
1.1 Bevel floating ball valves
A common bevel floating ball valve is shown in Figure 1. The valve seat is installed at a certain angle in the valve body, which is like a V shaped structure. This structure has the following characteristics:
(1) The sealing surface of the valve body is bevel, and a certain initial sealing force will be generated in the assembly process. The sealing performance between the valve seat, valve body and ball can be automatically adjusted.
(2) The installation and disassembly are convenient. When the pipeline needs to be repaired, only the valve bonnet needs to be removed for repairing and replacing the parts, which improves the use efficiency of the valve on the pipeline.
(3) There is a certain compensation effect. Generally, an elastic energy storage device is installed on the upper end of the ball for the ball valve with this structure to compensate for the defects of the sealing surface due to corrosion and wear, and to ensure the sealing performance. Although the bevel ball valve has a simple structure and reliable sealing and can meet the needs of our actual use, at the same time, the structure of the ball valve also has certain problems:
(1) Machining roughness is difficult to guarantee. It is difficult to directly process the bevel structure of the valve body on a CNC lathe, and it is difficult to achieve the required roughness for sealing with a CNC milling machine. In order to achieve the requirement for roughness, it is necessary to manually polish the bevel, causing unnecessary waste of human resources.
(2) The torque is great. In order to ensure the sealing of the valve, the tight fit between the valve body and valve seat as well as the valve seat and ball during installation will cause a great torque, and the torque is not easy to calculate.
(3) In the using process, the ball will move down due to wear and corrosion, causing seal failure and jamming.
Figure 1 Bevel floating ball valves
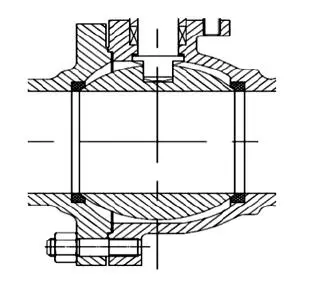
Figure 2 Side entry floating ball valves
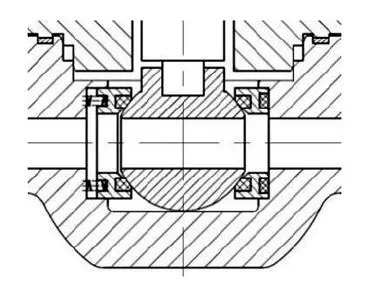
Figure 3 Top entry floating ball valves
1.2 Side entry floating ball valves
Figure 2 is the common structure of the side entry floating ball valve. The side entry floating ball valve has few parts, which has easy manufacturing and processing, easy assembly and disassembly, and good sealing performance. However, it is difficult to repair and maintain in time if it is installed on the pipeline. If there is a problem with the valve, even if only the middle gasket needs to be replaced, the entire valve needs to be disassembled from the pipeline and then repaired and replaced, resulting in a waste of costs. The side entry floating ball valve is not suitable for long pipelines.
1.3 Top entry floating ball valves
Figure 3 is the common structure of the top-mounted floating ball valve. Compared with the bevel floating ball valve, the matching part of the middle cavity of the top entry floating ball valve body and valve seat is a vertical plane, and the initial sealing force is provided by the spring. However, the assembly and disassembly process is troublesome and requires tooling for debugging. A set of special tooling is required for ball valves of different specifications and models, which increases the cost.