With the rapid development of modern petrochemical industry, coal chemical industry and refrigeration industry, cryogenic valves are used more extensively with a rising quantity. Therefore, how to use it correctly attracts users’ great attention. Except for those requirements for regular valves, there are also some other points needing be noted.
Cryogenic valves refer to those working under -29℃. Some of them can even deliver liquefied gas ( medium like oxygen, nitrogen, natural gas) at -196℃.
As the temperature of working medium drops, the material and structure of cryogenic valve, especially ultra-cryogenic valve, should be differed with regular valves. There should be some distance between the operating part and valve body, equipped with adiabatic device, to reduce the heat flux from outside. So cryogenic valves usually have a long-neck cover. Ultra-cryogenic valves work in a more complicated condition, from outside to the ultra-low temperature, and also are functioning continuously. Contact Pressure from sealing rings guarantee the seal of closing parts. But if the gear’s force is fixed, the strength, and the materials’ performance of sealing rings, especially polymers, may vary with the temperature. Therefore, ultra-cryogenic valves require strictly on the seal rings. STL is preferred.
As for ultra-cryogenic valve, the starting speed of its closing part is fairly limited. Even though heat insulation has been applied to it, there is still heat flux in a limited scope, which leads to the liquid formation in several parts. As a result, when the valve open rapidly, the liquid will get a great speed , and once it meets an obstacle like the valve, surge will be caused, which should be noted in use.
Iron valves, whose applied temperature scops from -28℃ to 150℃, used to be adopted to refrigeration, using nitrogen or Freon as refrigerant , but it is now used less. The use of fer-ritenodular iron remains on a positive growth instead, as a result of its great impact toughness, and corrosion-wear resistance.
The applied temperature range of WCB valves is -29℃~150℃, and the lowest applied temperature of LCB, LC1 & LC2 is -46℃~-73℃. Austenitic stainless steel (304, 316), known as a kind of low-temperature steel with good performance, can be used under -196℃, some even -254℃.
As for general cryogenic valves’ closing parts, metal sealings valves seats are applied to the body, fluoroplastic (F4) to the seat discs. It is almost the same in the structure as the general valves. The selection is according to the temperature&medium. The working feature is the only consideration for Cryogenic valves. It can be installed in any position inside the incubator, but with stuffing box, operation device( handwheel& wrench), and seats discs lifting position indicator outside the incubator for the convenience of operating and replacing the packing. And also, placing the stem horizontally is necessary for ultra-cryogenic electric valves, but not for most valves.
It is comparatively complicated for the feeder to work in low temperature.The filling is easy to lose elasticity. And once evaporative medium escapes and the stem is frozen, it will cause block and the valve cannot be open or closed normally. To improve this, thermal baffle can be installed to ensure the temperature of the fillings. One way is that the stem length should be increased and nonmetallic materials(textile, tap, and etc.), whose thermal conductivity is lower, be used to make baffle to significantly reduce the heat loss of the feeder. There is also another way, that is to cover the feeder and add some medium, which can keep the temperature applied for the feeder, to the space. It forms a temperature gradient between low temperature and working temperature, also among different working points, and then air pressure will be at a temperature that can make the liquefied gas return to gas.
Valve parts through manufacturing and testing at room temperature. When they work under low temperature condition, different parts will change because of changed temperature and will lead to different levels of expansion and contraction. This will directly affect the valve to work normally.
There are many kinds of Materials used in cryogenic valve. Common materials: such as carbon steel (WCB) will become brittle as the temperature changes.Most commonly used material is: austenitic stainless steel, bronze and copper nickel alloy, these materials are not easy to be brittle and they can ensure the normal use. Experiences show that austenitic stainless steel, bronze, copper and nickel alloy are of best toughness and strength. So some of cryogenic valve located in important parts, such as cut-off valve, relief valve, regulating valve, check valve and so on, all choose these kinds of materials.
Different materials of flange gasket, connecting bolt and fittings will lead to Shrinkage and not synchronous relaxation will cause leakage. Cryogenic valves in the process of assembly, especially those cryogenic valves that below -196 ℃, are better to be connected by welding.
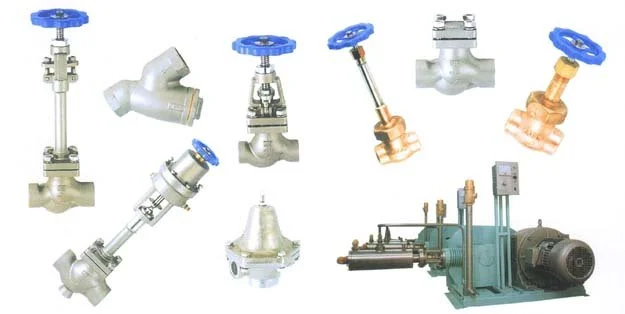