Differences between Y and Basket Style Strainers
Both Y and basket style strainers require isolating the strainers inlet and outlet to physically clean the straining element (thus interrupting the process flow), however there are significant functional differences that, depending upon specific application characteristics, will determine whether a Y or basket style strainer is best style for your application.
 |
Cast Y Strainer |
 |
Flow path through a Y Strainer |
Y Strainers
Although Y strainers are applied to liquid applications regularly, they were initially designed for steam, air and other inert gases to protect downstream equipment from a “particulate upset condition”; what we mean by that phrase is that normally particles are not expected, however as piping systems age bits of pipe scale, gaskets and other materials can become entrained in the process flow. Y strainers have a “blow down” port for this reason, bits of pipe scale can be “flushed” from the screen chamber by attaching a valve to this port and when opened to atmospheric pressure the material within the screen chamber is “flushed” through the valve.
The key takeaway about the design of a Y strainer is that it is designed to protect downstream equipment from material that isn’t continuously present in the process flow. Another way to describe this is that the percentage of particles to be removed from the process fluid should be relatively low if you are going to use a Y strainer.
There isn’t anything “wrong” about using a Y strainer for liquid applications; in-fact Y strainers have some advantages:
• They can be installed horizontally or vertically downward; basket style strainers can only be installed horizontally.
• They are more compact and thus less expensive than the basket style strainers.
• “Standard” Y strainers have higher operating pressure ranges than basket style strainers.
Perhaps the most significant downside of a Y strainer when compared to a basket strainer is the “open area ratio”. The open area ratio (OAR) is the ratio of the cross-sectional area of the inlet/outlet port compared to the open area of the element.
A straining element is either perforated or having a perforated substrate with a mesh lining for finer retention. Generally speaking, the finer the retention, the less open area the straining element has; why is this important? The percentage of open area combined with the flow coefficient (CV) of the strainer itself (design dependent) will determine the pressure drop across the strainer for a given flow rate. Generally speaking the higher the CV, the less of a pressure drop there will be across the strainer body; the open area of the straining element will determine how much more the initial differential pressure will increase.
Since Y strainers were not designed to continuously remove particulate, their design (strainer element chamber and element dimensions) are only designed to provide straining ratios of 1:1, 2:1 and perhaps in some cases 3:1, meaning at best the element has 3 times open area compared to the diameter of the inlet/outlet connection.
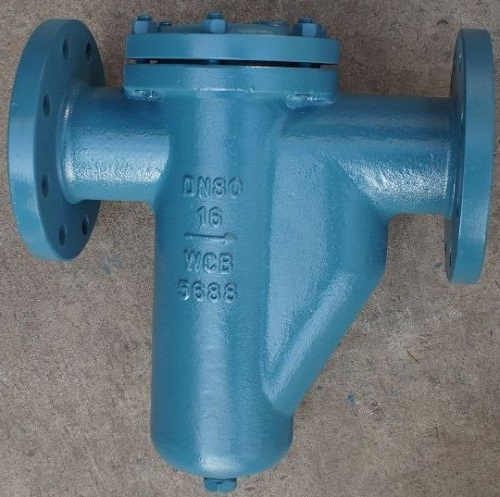 |
Cast Basket Strainer |
Basket Style Strainers
The phrase “Simplex Strainer” has become ubiquitous for basket strainers even though Y, Tee and other variations are also “simplex” in nature, so for clarity we’ll refer to them as basket strainers.
Due to the way the basket element “seals” in the basket chamber and the location of the drain port, they are designed to be installed horizontally. Although both Y and basket strainers are offered in cast and fabricated designs, the “standard” basket strainer design is typically rated for 150# or 300# pressure class applications whereas Y strainers are commonly rated to 600# - 2500# applications.
Getting back to the OAR aspect, the real differentiator, basket strainers typically have an OAR of 6:1 and sometimes as high as 8:1; significantly more than a Y strainer. This is why basket strainers are used for applications that have a continuous particle load. Thus an application such as reclaimed cooling tower water, where there’s an expectation of particulates that need to be removed all the time, is a better fit for a basket strainer than a Y strainer.
The difference in straining ratios is approximately the difference in frequency that the straining element will need to be cleaned, thus you would expect to clean a Y strainer screen that has a 2:1 OAR about 3 times as often as you would clean a basket strainer having a 6:1 OAR.
In summary, most liquid filtration applications that are either batch processes or where it’s acceptable to interrupt the flow to clean the straining element will be best suited for basket strainers due to their higher OAR and physically larger holding capacity. Y strainer applications are typically for inert gasses and for liquid applications where the particle loading is very low or only expected during an upset condition.