All diaphragm valves are bidirectional. They can be used as on-off and throttling valves. Diaphragm valves offer advantages in certain low-pressure applications not possible with other types of valves. Their fluid passages are smooth and streamlined, minimizing pressure drop. They are suitable for moderate throttling applications, and they exhibit excellent leak-tight characteristics, even when conveying liquids containing suspended solids. The fluid stream is isolated from the working parts of the valve, preventing contamination of the fluid and corrosion of the operating mechanism. Since there is no leak path around the valve stem, the valve is virtually leak tight. This feature makes the valve indispensable where leakage into or out of the system cannot be tolerated.
The maximum pressure that these valves can be subjected to is a function of the diaphragm material and the service temperature. Also, the rated design life of the valve is influenced by the service conditions. Furthermore, the system hydrostatic test pressure must not exceed the maximum pressure rating of the diaphragm.
Diaphragm valves (Fig. A) consist of a rigid body formed with a weir placed in the flow path, a flexible diaphragm which forms the upper pressure boundary of the valve, a compressor which is used to force the diaphragm against the weir, and the bonnet and handwheel which secure the diaphragm to the body and actuate the compressor.
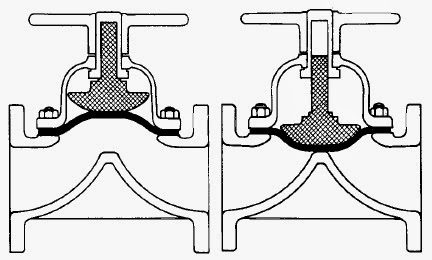 |
Fig. A: Sketch of a weir-type of diaphragm valve in open and closed positions |
Diaphragm valves are manufactured in a variety of end connections: welding end socket or butt welding; flanged, screwed, or threaded; clamp ends or grooved ends; solvent cement joint ends for themoplastic valves; and male sanitary threaded ends.
The valve body is available in two patterns: tee-pattern and angle pattern.
Diaphragm valves are available in a wide choice of body, diaphragm, and lining materials that are suitable for service with a wide variety of chemicals. For severe corrosive applications, diaphragm valves are made of stainless steel or PVC plastics, or they are lined with glass, rubber, lead, plastics, titanium, or still other materials.
Adjustable travel stops are used to prevent excessive compression of the diaphragm. The adjustable travel stop can be enclosed in a temper-proof housing. The temper-proof housing prevents inadvertent mishandling after the travel length is set. It requires a special tool to open the housing and to make an adjustment in the travel length.
When an actuator is required, it should be sized and tested by the valve manufacturer and furnished with the valve as an assembled unit with settings made and verified in the shop.
Primarily there are two basic designs of diaphragm valves: weir and straight-through types. The body interior and the end flanges can be lined to make the diaphragm valves suitable for corrosive applications. Various lining materials can be used, depending upon the application.
As shown in Fig. A, a weir is provided as an integral part of the valve body. The weir acts as the valve seat against which the diaphragm is compressed to stop the flow. This type of diaphragm valve is generally produced in large sizes. The raised weir reduces the amount of diaphragm travel from the fully open to the fully closed position, thus reducing the amount of stress and strain in the diaphragm.
Variations of the weir diaphragm valve are the straightway (Fig. B)
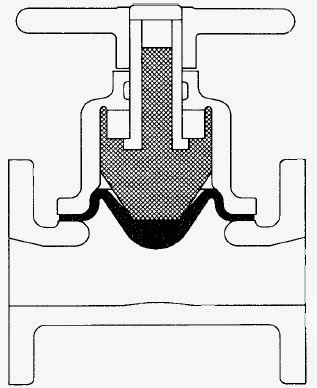 |
Fig. B: Straightway-type diaphragm valve |
and the full-bore types (Fig. C).
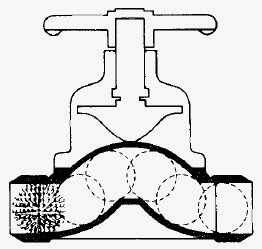 |
Fig. D: Full-bore-type diaphragm valve illustrating passage of ball-brush cleaner through valve |
When the straightway valve is open, its diaphragm lifts high for full streamline flow in either direction. When the valve is closed, the diaphragm seals tight for positive closure even with gritty or fibrous materials in the line.
The full-bore type of valve is most extensively used in the beverage industry. It permits ball-brush cleaning with either steam or caustic soda, without opening or removing the valve from the line.
The following summarizes some distinct advantages of diaphragm valves:
1. Can be used as on-off and throttling service valves.
2. Offer good chemical resistance due to variety of linings available.
3. Stem leakage is eliminated.
4. Provides bubble-tight service.
5. Does not have pockets to trap solids, slurries, and other impurities. It is suitable for slurries and viscous fluids.
6. These valves are particularly suitable for hazardous chemicals and radioactive fluids.
7. These valves do not permit contamination of flow medium, thus they are used extensively in food processing, pharmaceutical, brewing, and other applications which cannot tolerate any contamination.
1. The weir may prevent full drainage of piping.
2. Working temperatures and pressures are limited by the diaphragm material. Generally the pressures are limited to 200 psi (1380 kPa) and temperatures up to 400 F (204 C).
3. The diaphragm may also limit the hydrostatic pressure.
4. The diaphragm may experience erosion when used extensively in severe throttling service containing impurities.
5. Diaphragm valves are available in limited sizes, usually NPS ¹⁄₂ to 12 (DN 15 to 300).
1. Clean or dirty water and air service applications
2. De-mineralized water systems
3. Corrosive applications
4. Radwaste systems in nuclear facilities
5. Vacuum service
6. Food processing, pharmaceutical, and brewing systems
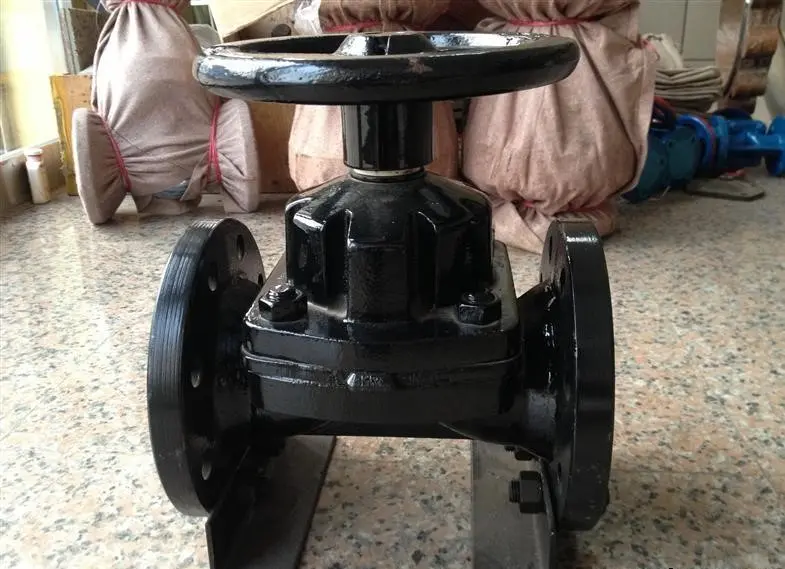